Tips to Avoid Detention Charges in Shipping and Make Carriers Happy
.jpg)
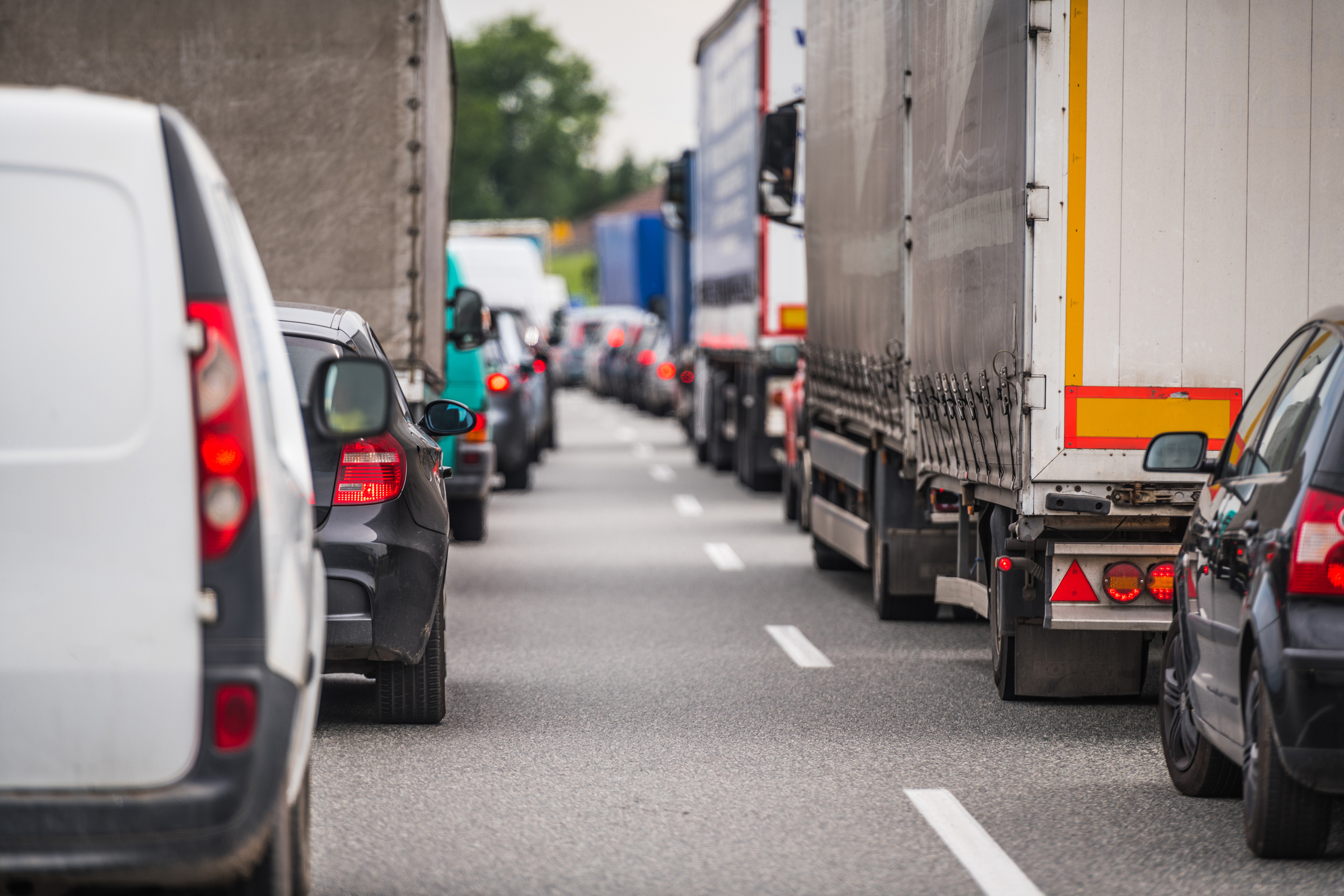
Many individual factors have to come together comprehensively for modern shipping and transportation services to flow effectively. Everything from loading restrictions, capacity and driver shortages, rising shipping costs and fuel rates, and detention charges in shipping can all impact end-to-end supply chain operations. But of all these, detention charges are some of the most difficult to plan for and manage. Understanding detention, surcharges, and shipping trends is critical for smooth network operations in both the short and long term. Maximizing freight matching services is vital for continued growth and success. Here are a few tips to avoid detention charges in shipping and to make your carriers happy and more willing to accept freight from your company.
In the most simplistic of terms, the shipping industry charges additional fees when delays or other issues occur. These are called “detention charges” and “per-diem charges,” though the term “per day charges” can also mean the same thing. Generally, per-diem and demurrage are reserved for movements nearest a port, but both detention and dwell time charges can be assessed when a carrier spends too long waiting to load or unload a shipment at a port, distribution center, or another location.
When a container remains at port for longer than expected, beyond the free time period, the port authority may leverage detention charges against the cargo owner. Detention charges in shipping may also apply when a carrier determines dwell time waiting at a warehouse has become unreasonable and bills the shipper for the wasted idle time. Again, individual carriers may have different terms used based on their preference. For instance, owner operators may lump all extra fees like these under a broad detention charge name. However, they’re usually reserved for failures in planning drayage to ports for moving containers. That’s why shippers need a better strategy for capacity management to ensure individual delays do not amount to major costs like detention charges in shipping.
Detention charges in shipping and a few other expenses are avoidable to a certain extent, though it takes a great deal of planning and managing to do so efficiently. Regardless of who caused the delay, the cargo owner/shipper usually foots the bill and must pay the detention charges. According to Hellenic Shipping News Worldwide, when shippers hold on to containers for a long time, it can create bottlenecks at the docks and delay vessels that could otherwise be reloaded and sent out on another trip. The detention surcharge is intended to discourage ocean carriers and importers from waiting until the eleventh hour to move containers off the dock. However, faster drayage planning inherently means shippers need a better strategy procuring drayage, and it also implies a degree of improved transportation asset management for carriers.
Obviously, detention charges in shipping are something to avoid as much as possible. But how can shippers reduce charges and fees and gain shipper-of-choice standing within the supply chain? Following these tips can help with logistics and management:
- Know lead time expectations. Planning and giving enough lead time for loading and unloading remains a critical first step toward solutions.
- Reduce reliance on spot trucking. Long-term contractual shipping is easier to plan for and also easier to monitor for possible delays.
- Leverage data to understand actual dwell time. Employ real-time tracking and monitoring processes and tools to see when and where delays happen most often.
- Eliminate inconsistencies with centralized controls. Avoid delays caused by poor communication and data sharing by automating the entire process.
- Boost confidence with digital load boards to post loads. Utilizing online tools and platforms can help ensure loads keep moving as efficiently as possible.
- Take advantage of expert guidance in managing drayage too.
Many of the tools used for avoiding detention surcharges can also help reduce drayage and demurrage fees too. - Know the policies of port authorities.
Every port has slightly different regulations and timetables, so checking ahead for carrier resources remains critical. - Work with experts that can combine storage and transport closer to port. The less handling a container requires, the faster it can be unloaded and returned to the port.
- Consider other new technologies, like AI, RPA, and app-based procurement tools— such as Edge CAPACITY—to reduce confusion and improve collaboration. Using modern technologies will enhance cooperative efforts and help avoid the risk of detention charges.
Together, these steps effectively ensure your team is more likely to move containers off the dock faster, return them faster, and keep things rolling—quite literally. But that often comes down to ensuring your transportation service partners are able to do so. But again, it depends on how easy it is for them to get the container, take it to your next facility, have it unloaded, and then returned to the port. In other words, your freight needs to be easy to unload, and your information needs to be detailed. Without details, your partnering carriers will inevitably grow frustrated, spend more time than needed handling your freight, and be less likely to work with you. However, the tips detailed above have the reverse effect—making your freight more attractive to carriers and opening the doors to shipper-of-choice status.
To help improve the entire shipping process and avoid detention charges in shipping, shippers need to improve their relationships with carriers. They can achieve this goal by leveraging innovative tools and collaborative platforms. That comes together to help shippers attain shipper-of-choice status, keep carriers happy, and ensures your freight always has coverage that you can count on. Be part of the solution to overcoming the risk of detention charges and extra expenses by contacting Edge Logistics today.
About the Author
.jpg)
Pamela Nebiu
Pamela is the Senior Marketing Manager at Edge Logistics. She has a Bachelors of Arts from DePaul University in Public Relations and Advertising with a minor in Photography. Pamela is responsible for overseeing advertising, marketing, press, and social media related to Edge.